IoT Basics for Fire Suppression Systems
Fire suppression systems will typically be in service for a decade or more without the need for updating or changing out once installed. As a result, many fire suppression systems are not currently equipped to take advantage of certain recent advances in technology, especially when it comes to leveraging data.
Data has become one of the most valuable commodities to ever exist, and almost no business can afford to neglect it if they want to be competitive in the marketplace. Integrating sensors into key components makes it possible to easily collect, analyze, and aggregate data in ways never before possible. Building and facilities monitoring dashboards can collect and display critical information on systems such as natural gas and electricity consumption as well as HVAC system health and status. In fact, the HVAC industry was relatively quick to adopt integrated sensing technologies to monitor their systems and collect the appropriate data. But the fire suppression industry has not yet fully understood the benefits of data collection and integrated sensing, and OEMs have been slow to explore adding integrated sensing to their systems.

Fire suppression systems that take advantage of integrated sensing and data collection stand to see major improvements in safety and efficiency. For example, fire suppression systems are typically inspected only twice per year. Faults might only be detected during these biannual inspections, jeopardizing the efficacy of the system. More than that, a fault that may eventually result in complete system failure, such as a leaking valve that may eventually completely discharge the system, may not be detected between biannual inspections. This means that repairs may only be made either because of inspection or after system failure. But with the appropriate sensors integrated into key components, minor faults can be detected as they occur and be corrected before the system is rendered inoperable.
Human error has been a significant factor that has hampered the safety and operability of fire suppression systems. For example, due to instances where technicians had either forgotten to reinstall an actuation device after maintenance or had incorrectly installed the actuator, rendering the system incapable of firing, NFPA 2001: Sec. 4.3.4.1 requires an audible and visual alarm anytime an actuation device is either removed or improperly installed on the discharge valve. This supervision standard has greatly reduced the instances of human error during installation and maintenance. But integrated sensing can do so much more to improve system safety.
If the system’s extinguishing agent storage tanks do not have the proper amount of agent, the system cannot discharge properly. Most methods of determining the weight of the extinguishing agent require technicians to manually measure the level of agent and then calculate the weight using a conversion table. This manual process creates the potential for errors. With advances in integrated sensing, it is now possible to automatically provide a thermally compensated weight reading of the extinguishing agent in each individual storage tank and have that measurement visible directly at the tank, at the fire control panel, or even displayed remotely via wireless connection, without the potential errors that could result from manual calculations.
Integrated sensing can be added to a system’s actuators as well. Sensors can measure voltage, current, the position of the firing pin, and if the actuator is fully installed on the discharge valve to ensure that the system is capable of firing. Sensors can log when the actuator has been removed for maintenance, and X, Y, and Z shock axes can also be recorded. This can help determine if the actuator was manually activated or if an accidental discharge occurred due to impact to the actuator, perhaps from a forklift moving equipment around the facility. System fire and system test data can be logged for liability and insurance records. All this data would include a time stamp that can track system status, record maintenance, and be used to determine liability.
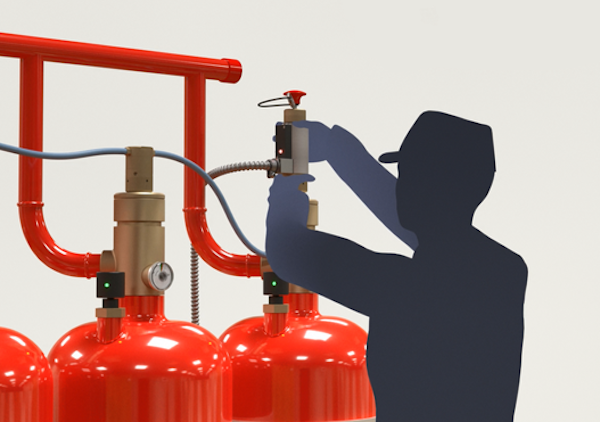
These sensors can be retrofitted to existing systems or installed as part of a new system. All the data they collect can be examined on-site or remotely via wireless connection. This capability is especially critical in an age where remote work has become increasingly common, and the effects of COVID-19 have often resulted in fewer personnel on-site. And for remote sites that are in areas that are difficult to access such as power substations, telecom shelters, and offshore liquid natural gas and oil rigs, this type of technology is an economical way to have constant monitoring of the fire suppression system at only a fraction of the cost of the actual system itself.
It is important that all stakeholders begin considering how this technology can be best implemented to bring the greatest benefit to the fire suppression industry so that the best solutions can be developed and implemented. If fire suppression OEMs consider input from their customers and take advantage of the integrated sensing technologies that are available to the market, they can make their systems safer, more reliable, and improve the efficiency of system maintenance while adding considerable value to their systems at minimal cost.
This article was originally published by TLX Technologies in June 2022