The Value of Combining Sensing Integration and Mechanical Innovation
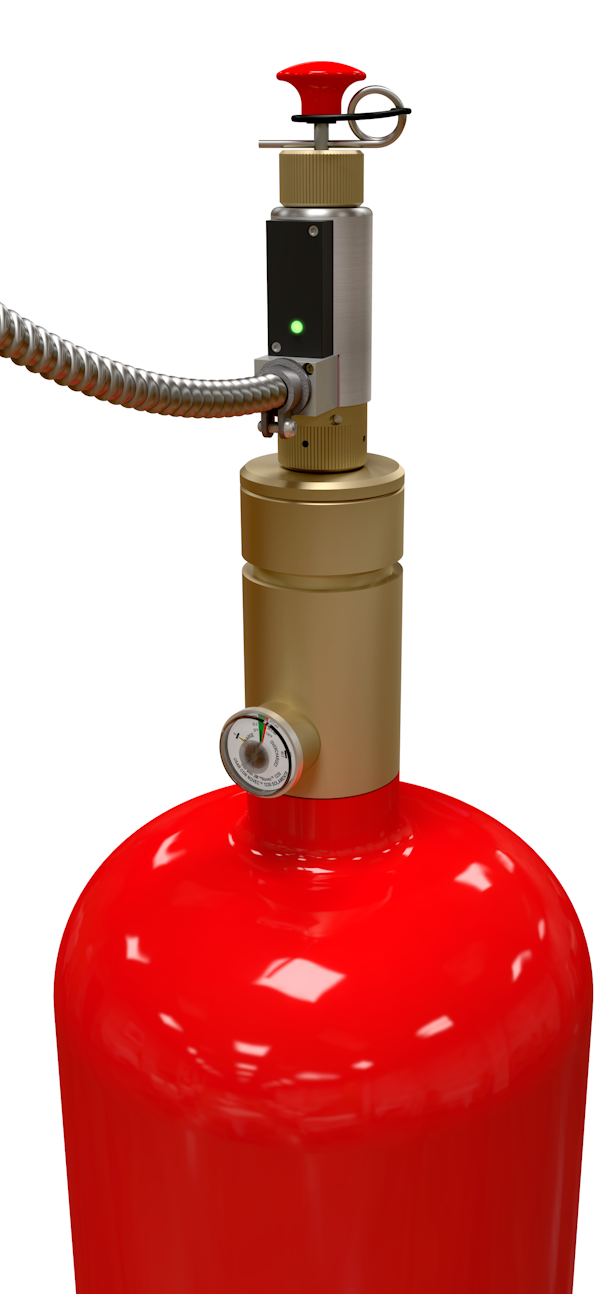
Sensing, data collection, and the Internet of Things (IoT) is increasingly becoming a common place part of everyday life. Everything from refrigerators to complex manufacturing equipment utilize a combination of these technologies to make people’s lives a little easier. These technologies, when properly implemented, hold considerable value for the fire suppression industry. Sensing and data collection can help with everything from improving the efficiency and safety of system maintenance to risk mitigation. Remote connectivity allows this data to be shared across systems so that the overall system health can easily be monitored both on site and remotely. This is becoming an increasingly crucial necessity in an era where COVID-19 has resulted in fewer employees being consistently on site. Combining mechanical innovations with sensing, data collection, and remote connectivity can create the safest, most reliable system possible.
We will explore some of the products that can make a fire suppression system safer and more reliable, and how sensing and remote connectivity can add value to the fire suppression system.
Facilities that house assets that would be water damaged by traditional sprinkler systems will often rely on gaseous fire suppressions systems. The gases used in these systems are stored in pressurized tanks. When the system is activated, an actuator releases the suppressing agent into the protected area. This extinguishes the fire by reducing the oxygen content or temperature to the point where combustion is no longer possible. The primary device used for releasing the suppressing agent from the storage tank is the electric latching actuator.
These actuators must be correctly installed on the discharge valve of the storage tank for the system to discharge in the event of a fire. Human error can be a major contributor to system malfunction. A number of incidents have been documented where technicians had either improperly installed or entirely failed to install the actuator onto the discharge valve during system maintenance. These errors rendered the fire suppression systems inoperable, leading to a critical safety hazard. In response, NFPA 2001: Sec. 4.3.4.1 states that such actuators must include a supervisory feature that sends an audible and visual signal to the fire alarm control panel (FACP) when the actuator is removed from the discharge valve. These signals are only deactivated when the actuator is properly installed. This provides a critical safety check during system maintenance, reducing the likelihood of human error disabling the fire suppression system.
In response to the NFPA requirement, many companies designed add-on supervisory components for their existing actuators that could be connected to the fire suppression system. But these add-on components create additional complexity and new potential failure modes.
When TLX Technologies designed their supervised latching solenoid actuators for fire suppression systems, they believed that integrating the supervisory feature into the actuator was the best solution. This makes the actuators easier to install and use than other solutions that rely on add-on components to fulfill the supervision requirement. TLX’s actuators provide fully-engaged installation detection without the need for additional components or electrical connections. They are resettable for future use and are UL Recognized Components. They are also designed so that optional integrated sensing features can be included based on the customer’s needs, which will be discussed later.

Because each fire suppression system has its own unique operating pressures, TLX offers supervised electric latching actuators to meet the requirements of any system with operating pressures up to 300 bar.
While these actuators are suitable for general gaseous fire suppression systems, they are not suitable for hazardous locations where the possibility of flammable materials in the atmosphere (such as in a hazardous gas environment) might cause a spark from the actuator itself to ignite a fire. Hazardous locations require actuators with specialized design features to prevent this from happening. Ideally, they should also include an integrated supervisory feature.
TLX has developed the Explosion Proof Actuator with Supervision, which is UL HazLoc, ATEX, and IECEx certified for use in hazardous locations. It has the same integrated supervisory feature, providing fully-engaged installation detection, and its force output can also be customized to accommodate systems with operating pressures up to 300 bar.
The Explosion Proof Actuator with Supervision is uniquely designed as a top-mounted linear actuator, so it does not act as a pressure vessel on the discharge valve. This design feature helps to reduce the number of potential leak points in the system. This provides a distinct advantage over systems that use a combination of pneumatic and electric valves, which result in multiple leak points due to the number of connections required to route discharge pressure through the system.
Specific design features and material grade selection were included to allow the actuator to also act as an enclosure, eliminating the need for additional components. If a spark were to ignite any gas found within the actuator, external flame propagation is prevented. All potential flame paths are specifically designed to stop flame egress.
Additionally, every actuator features fully customizable interface options. They can be made with either male or female connectors with customizable thread size and thread count, and the actuator assembly can fully rotate for easy installation. The firing pin stick out and stroke length can also be customized to match system requirements.
Electric latching actuators alone are often not enough for the needs of some fire suppression systems. Systems that rely on multiple storage tanks need a means to release the suppressing agent in all the tanks simultaneously. The Pneumatic Actuator, when mated with one of the electric latching actuators, offers a full system solution.
The Pneumatic Actuator, like the electric latching actuators, is a top-mounted actuator that, instead of relying on an electrical connection to activate, uses some of the discharge pressure from the master storage tank to actuate. An electric latching actuator is installed on the master storage tank, and when the system is activated, some of the discharge pressure is routed to the pneumatic actuators through a hose. This pressure causes the pneumatic actuators to mechanically open the discharge valves of the storage tanks on which they are mounted.
The inclusion of the Pneumatic Actuator improves the cost effectiveness of the system because only one electrical actuator is required to discharge a multi-tank system. Activation of just the master storage tank automatically discharges all the storage tanks.
Should there be a need to activate the fire suppression system manually, an optional Manual Release Cap can be added to any of the electric actuators and is available in three configurations: push button, lever action, and pneumatic lever action (for use with systems with pneumatic actuators).
While integrating supervision along with these mechanical innovations helps end users improve the safety and reliability of their fire suppression systems, additional integration of sensing, data collection, and remote connectivity can complete the package and bring the best value, depending on system requirements.
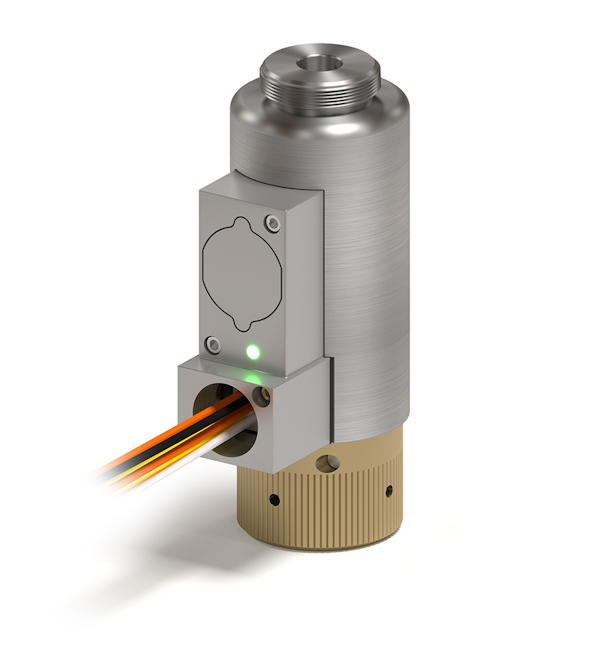
Integration of the supervisory feature was of primary importance. Virtually all fire protection systems need fully-engaged installation detection to satisfy NFPA requirements. But technology allows for additional sensing and data collection options.
The Pin-State Indicator feature can be added as an upgrade to all newly manufactured TLX fire protection electric actuators (except for the Explosion Proof Actuator with Supervision) and uses an LED to indicate firing pin position prior to installation of the actuator. This indicator ensures that the firing pin has been reset prior to installation, mitigating the risk of accidental discharge. The LED can be powered by a battery, so there is no need for additional wiring.
Finally, the Event Recorder can be integrated with any electric actuator that is compatible with the Pin-State Indicator. It logs a time-stamped history of events, including proof of proper installation and other valuable data such as ambient temperature, voltage, current, acceleration (X, Y, and Z axis) and firing pin position. This provides critical information about system health and why the system activated. The accessibility of data is configurable to meet the customer’s requirements.
Utilizing one of more of these sensing or data collection technologies, integrated to the right actuator, can reduce system complexity and allows for both remote and on-site real-time monitoring of overall system health. It also makes system maintenance easier while improving safety. The risk of accidental system discharge or incorrect actuator installation is mitigated, and real-time monitoring of system health ensures that if a problem does arise, quick action can be taken to bring the system back to full operation.
This article was originally published by International Fire & Safety Journal in September 2021